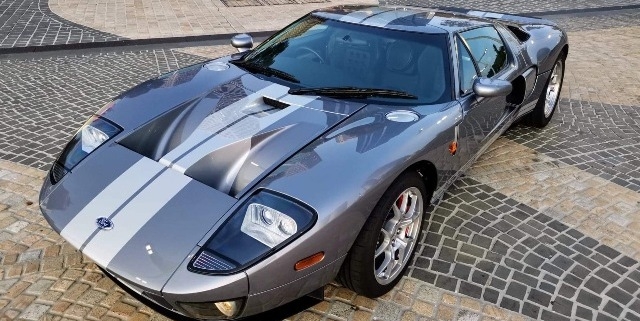
If you have visited Perth, Western Australia, you may have caught a glimpse of this sleek, liquid grey icon of Performance Motorsports plying the city’s streets. Back in 2014 the Ford GT40 Supercar required conversion from left to right-hand drive and Routers Australia was commissioned to complete the structural work required . Think reverse engineering.
The project involved re-engineering various parts including the foot well, dash mould and centre console. Work included creating moulds, hand forming aluminium and 5-axis CNC machining, as well as digital 3-D scanning and 3-D printing.
As a point of interest, although officially named the Ford GT, this car has always been known, of course, as the Ford GT40. This was originally more of a nickname and was never registered by Ford. When they went to name their modern GT’s GT40’s someone else had acquired the copyright & wanted them to pay through the nose to use it. However the name has stuck and the legend lives on!
Then and Now…
Fast forward to August 2020; enter Project GT40 Part II. It seems that our cars’ proud owner just couldn’t get enough of a good thing. Therefore we will soon be repeating this work for a second GT40–and this time it’s liquid red. Baby! (Note: liquid grey and liquid red are two official GT40 colours)
This time we will be using some of the forms we created for the initial project such as the solid wood buck pictured below. Traditionally these are made for the purpose of hand forming metal for body building cars.
The Foot Well
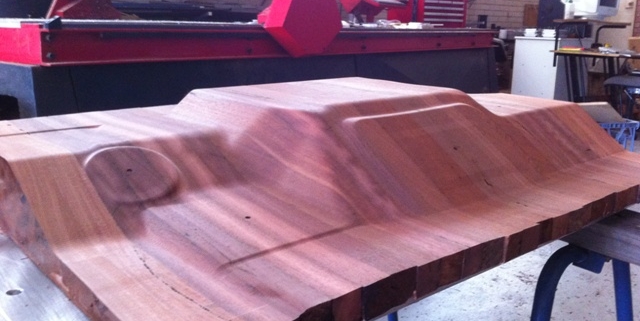
We were able to create this buck for forming the aluminium foot well using 3-D laser scanning. With the help of 3-D CAD and CAM software programs it was then possible to machine this beauty on a 5-axis CNC Router.
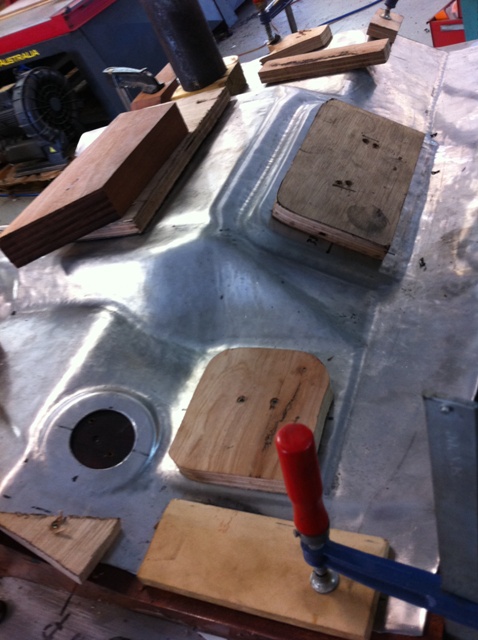
Hand forming the aluminium sheet over the wooden buck is a time consuming job requiring skill and patience. The metal can easily be irrepairably damaged while being beaten into shape. It must be repeatedly annealed (heated to a certain temperature to soften) throughout the process due to work hardening, where the metal becomes harder and more difficult to shape as a result of the hammering. This particular job required about two days work.
After shaping, the cutouts are then done on a 5-axis CNC Machine to allow for the various cutting angles.
Below is the foot well complete with cutouts, ready to be installed.
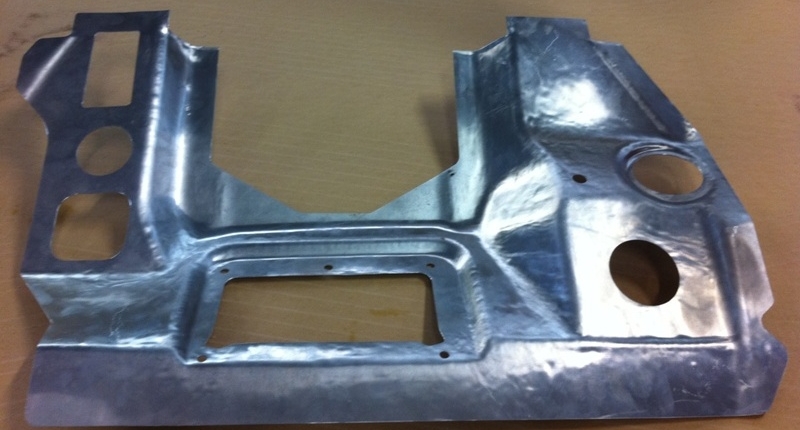
The Central Console
Using a 5-axis CNC, the central console was machined from solid aluminium block down to a thickness of three to nine millimetres all over. This section (below) has been sand blasted ready for welding onto the rear section of the original console.
This time around the whole console will be machined from one solid block.
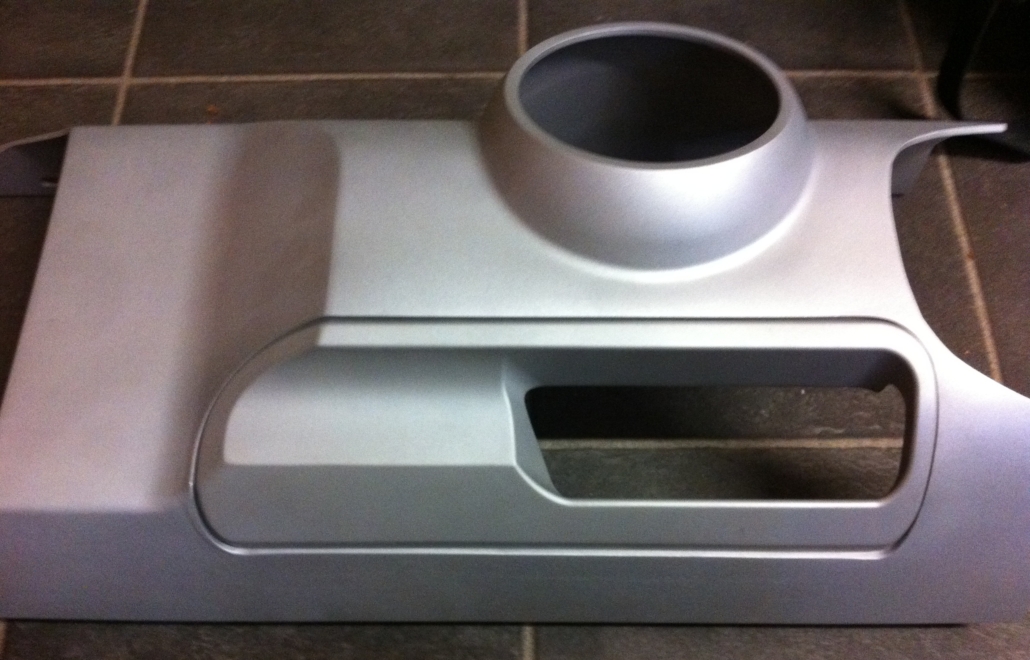
In Conclusion
Watch this space. We will be posting updates and videos of our new project once we are rolling.
Editor’s note: Methinks, this happens to be a cool project for someone who was a very successful Junior when he was getting around WA’s Go-Kart racing circuit in his hand-built machine at the age of 14–16. He then went on to build WA’s first V8 powered FJ Holden when 16–18 years old. That would be our Managing Director, Graham van Zuilecom.
Routers Australia is a uniquely versatile engineering company. We will work together with you providing expert advice, knowledge and skill throughout the process to complete your project. With an extremely broad range of experience and a passion for excellence in all we do, we are confident that we will deliver solutions over and above your expectation. Contact our team for a quote today!